Company profile |
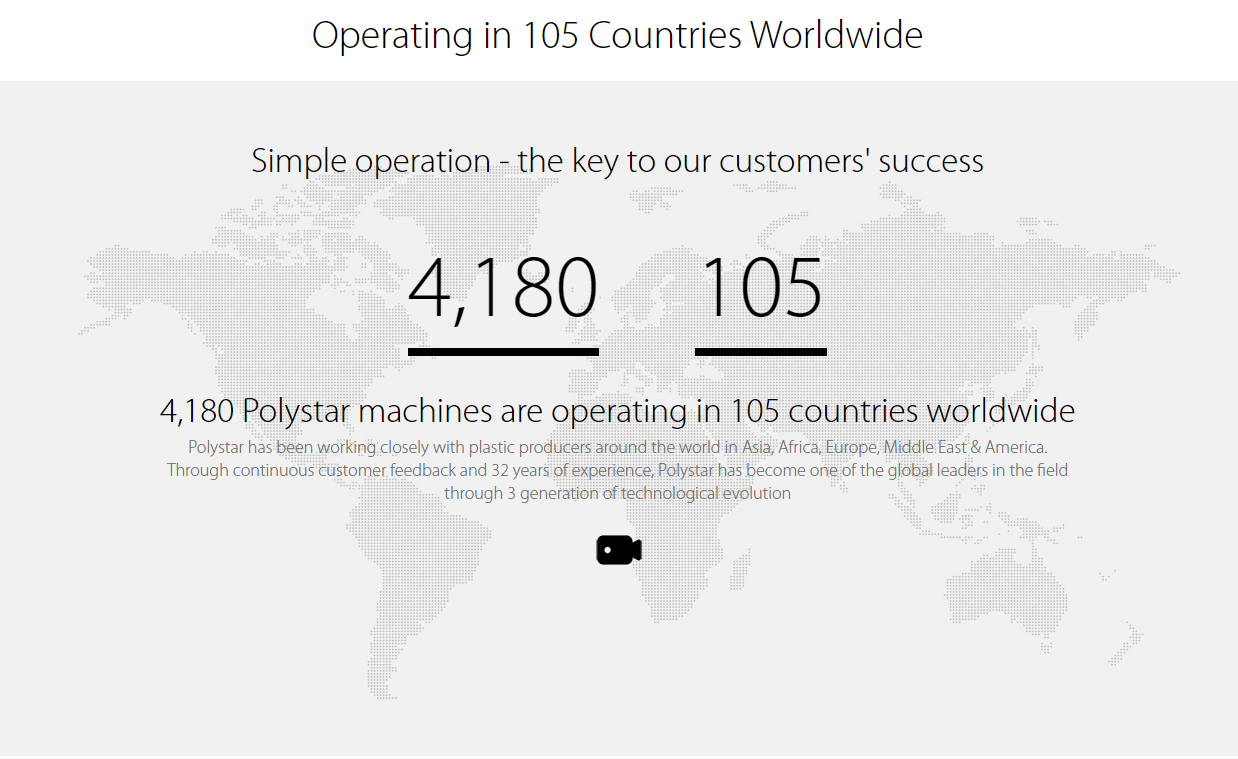 |
33 years of experience Through years of manufacturing and designing experiences and continuous customer feedback, POLYSTAR has become one of the global leaders in the field through 3 generation of technological evolution.
A global leader with 4,180 machines installed More than 4,180 machines have been installed since 1988. Proven success in Asia, Africa, Europe, Middle East & America.
Satisfied customers in 105 countries POLYSTAR has been working closely with plastic producers around the world and has established itself as a premium brand that offers reliable and high performing machines in the market. |
 |
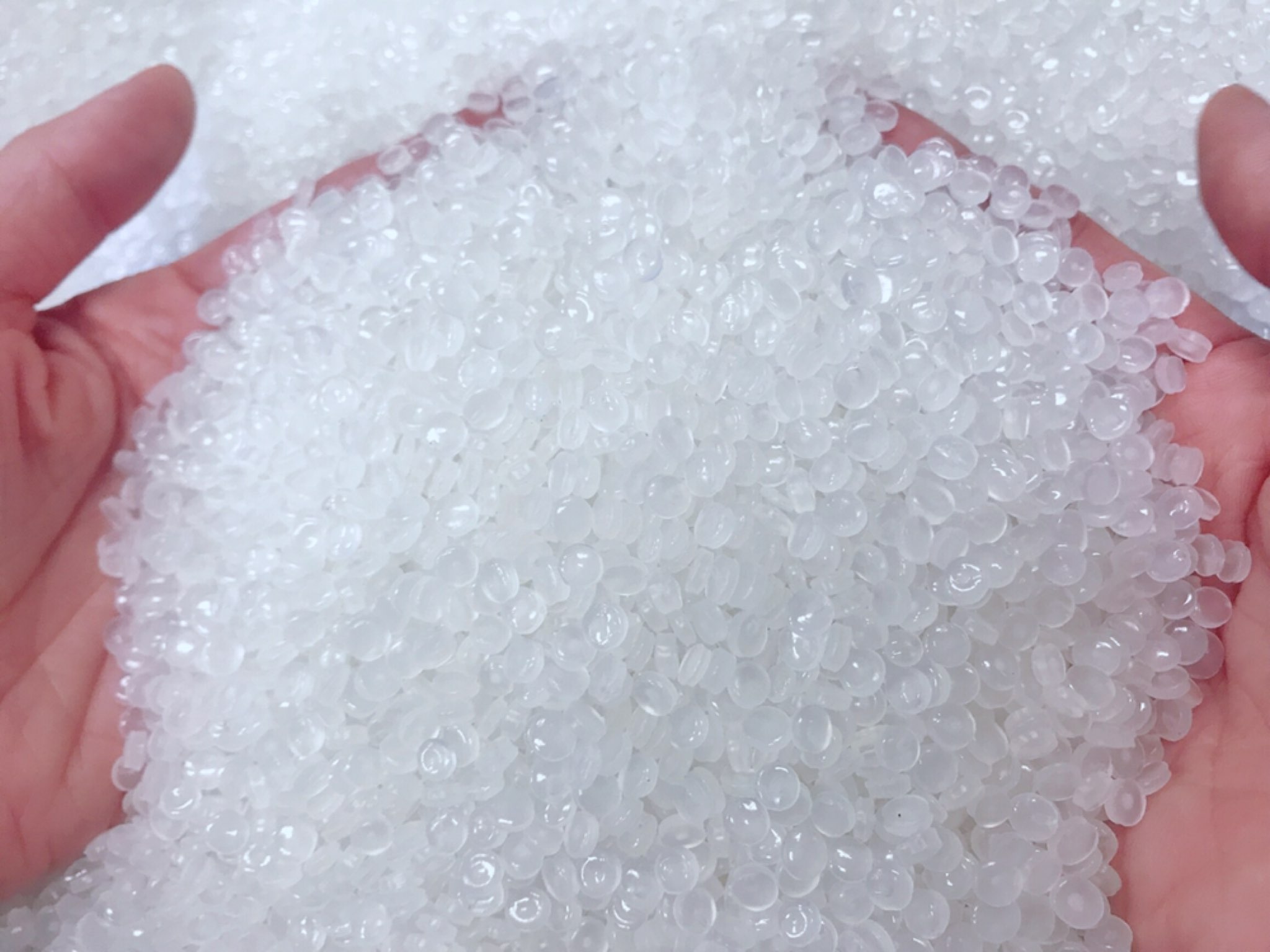 | High quality recycled pellets Up to 100% reusability back into your production line. Post-industrial waste generated from production of film, raffia and injection regrind can be recycled efficiently by Post-industrial Plastic Reprocessing Facility and put right back into your production lines. Meaning less amount of new (raw) material needs to be used in your production. |
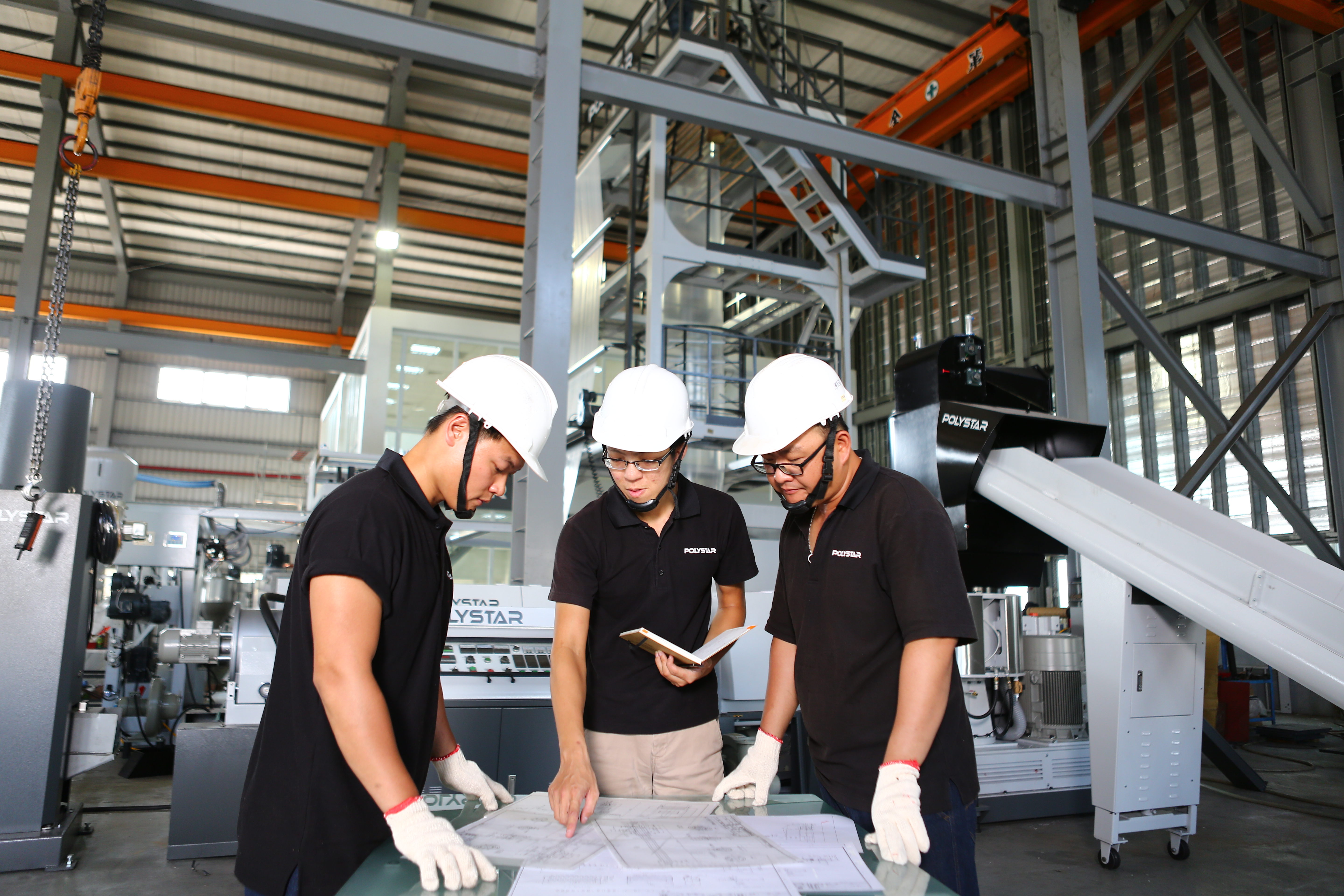 | Manufacturing with Precision - CE certified Post-industrial Plastic Reprocessing Facility with total quality control - Adopts the latest design and manufacturing of screw and barrel to achieve maximum efficiency - Strong research and design team |
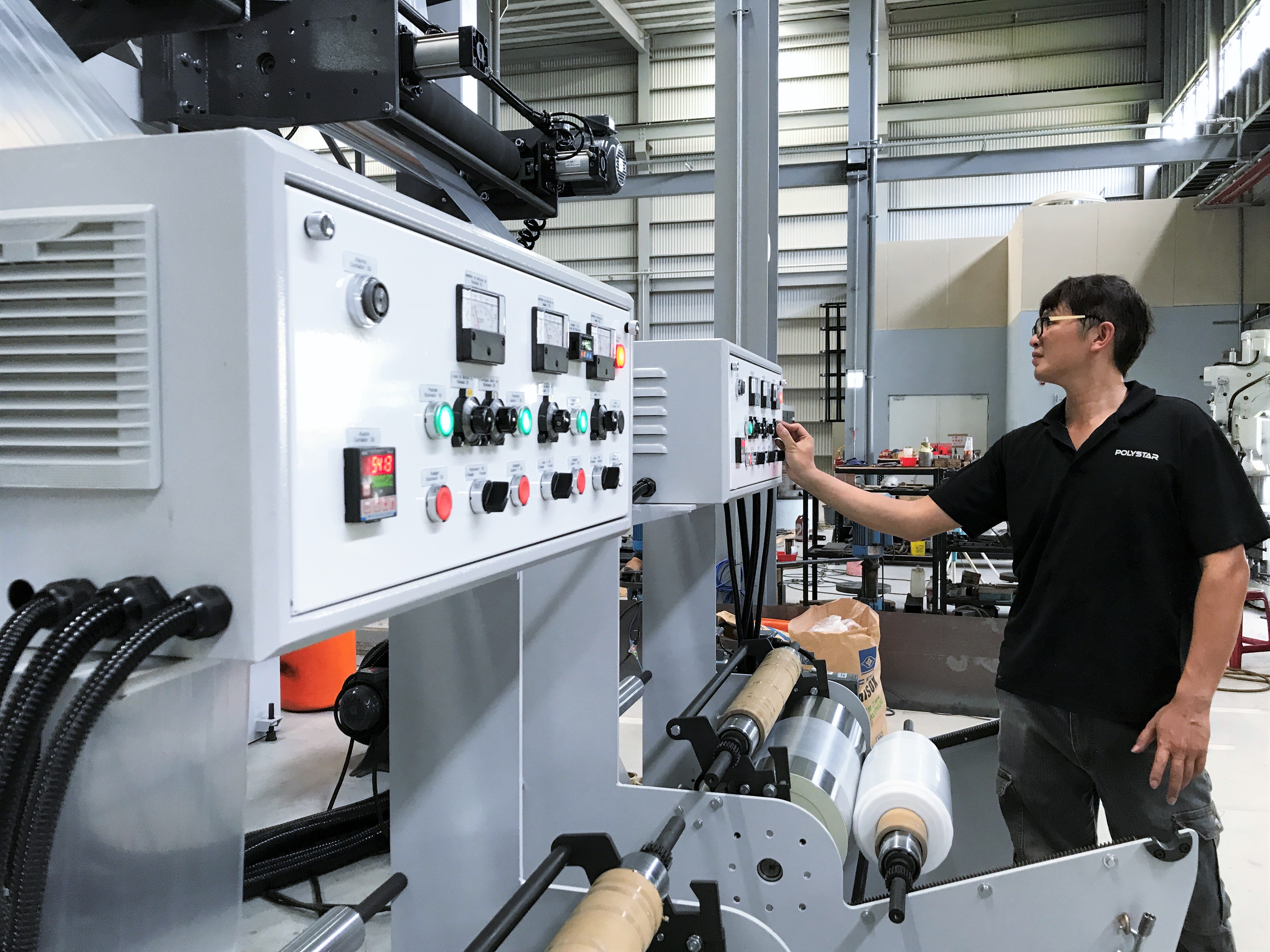 | Service and Communication - Overseas Post-industrial Plastic Reprocessing Facility installation service and training are available - Machine warranty with in-time spare parts delivery - Fast online trouble shooting |
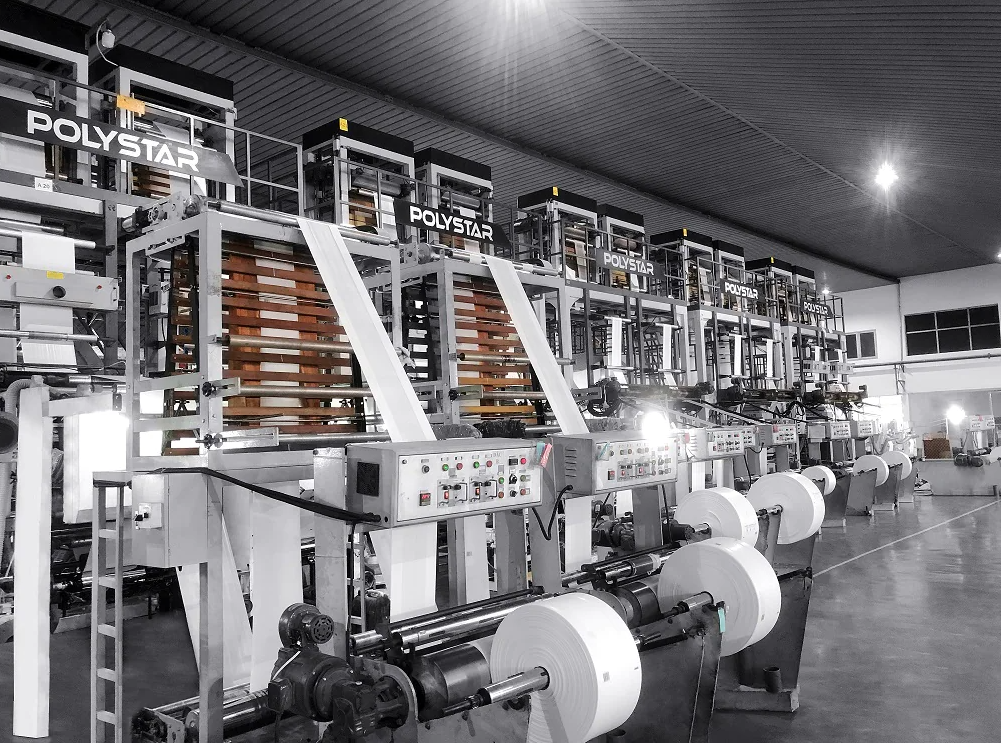 |
Film Production Industry |
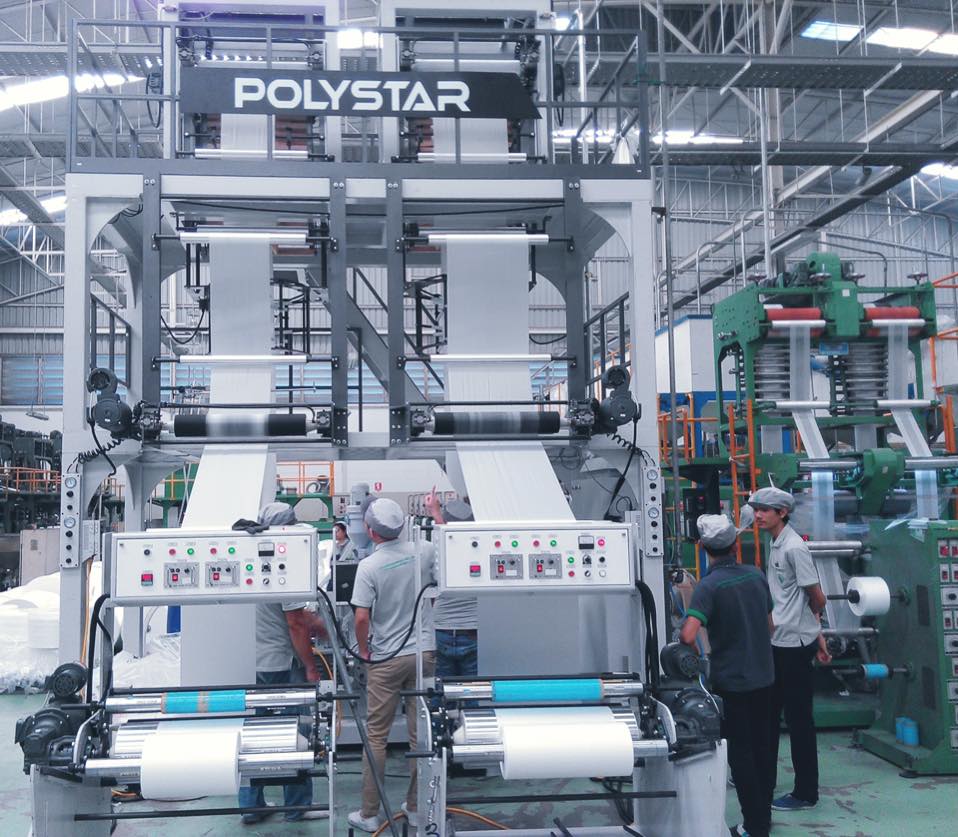 | 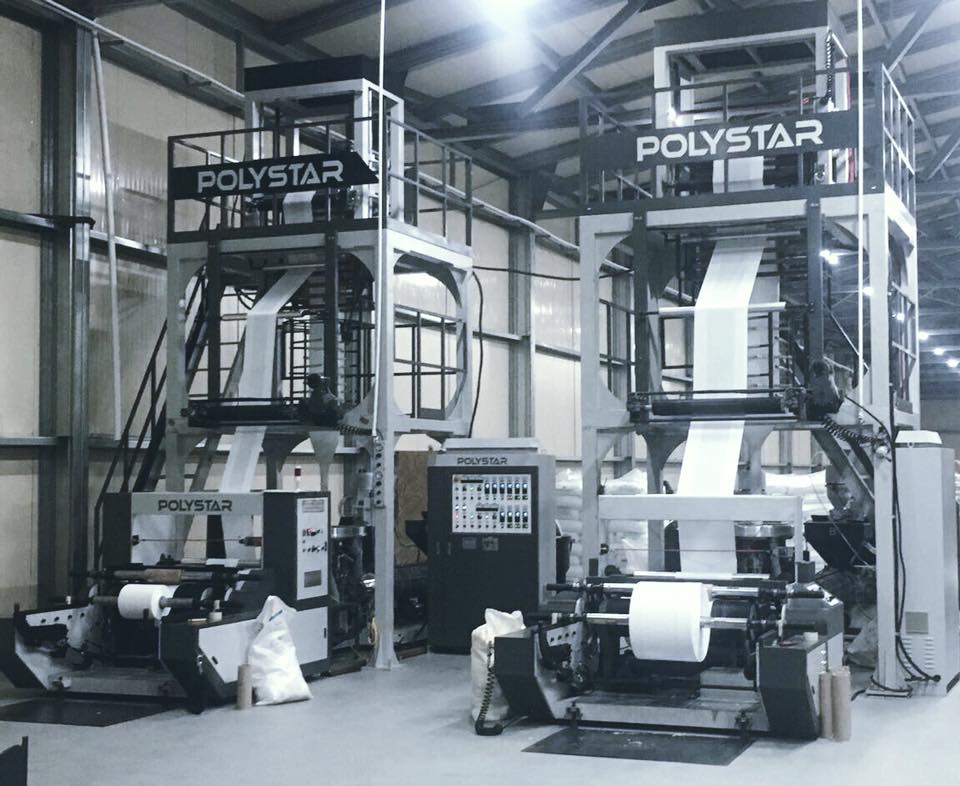 |
T-shirt bag producer | Carrier and DHL bags |
Vietnam The Vietnamese bag producer with monthly production of 1,500 tons doing 100% export to mainly European and Japanese markets. HDPE thin T-shirt bags with virgin material for the Japanese market and LDPE thicker garbage bags (bag on rolls and draw tapes) with recycled material for the European markets can both be produced on the same DM55-750 machine. The switch between producing HDPE/LDPE can be done simply by changing the die heads and air rings of the machines. Space saving, lower energy consumption, higher productivity are the reasons why the company continues to invest in POLYSTAR every year for both quality product and manufacturing efficiency. | UAE Sharjah-based bag producer who manufactures LDPE two layer (AB) carrier bags, DHL bags, high quality shopping mall bag, soft loop handle and many others. Load cell tension control, edge position control, 4 component gravimetric dosing and fully automatic double winding and cutting are equipped to improve manufacturing efficiency and automation. Film thickness from 40 micron to 150 microns, and film width from 700 ~ 1300mm can be achieved in this machine depending on the product requirement. |
 |
Recycling Industry |
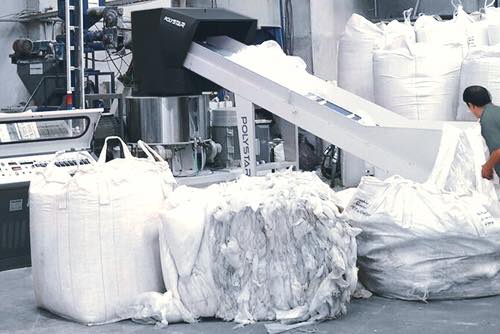 | 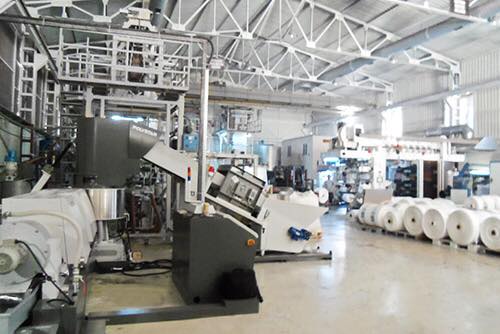 |
Thermoforming - PS, PP cups, trays producer | BOPP and laminated film producer |
Bolivia Production waste from thermoformed PP trays, cups, spoons and PS utensils. The largest plastic producer located in Bolivia with over 2,000 employees is currently recovering all of its industrial waste with two POLYSTAR recycling machine HNT-120V, processing in total of 1,000 kg/hour. The recycling machine can flexibly handle both PP and PS thermoformed product, in addition to some of the PE and PP film waste. | Canada BOPP and stretch film scraps and film on-roll can be turned into high quality pellets for reprocessing. POLYSTAR’s advanced cutter-compactor system can process material that is typically more difficult to recycle due to its special property, such as printed BOPP and stretch film that one normally faces problem with the traditional recycling systems. |
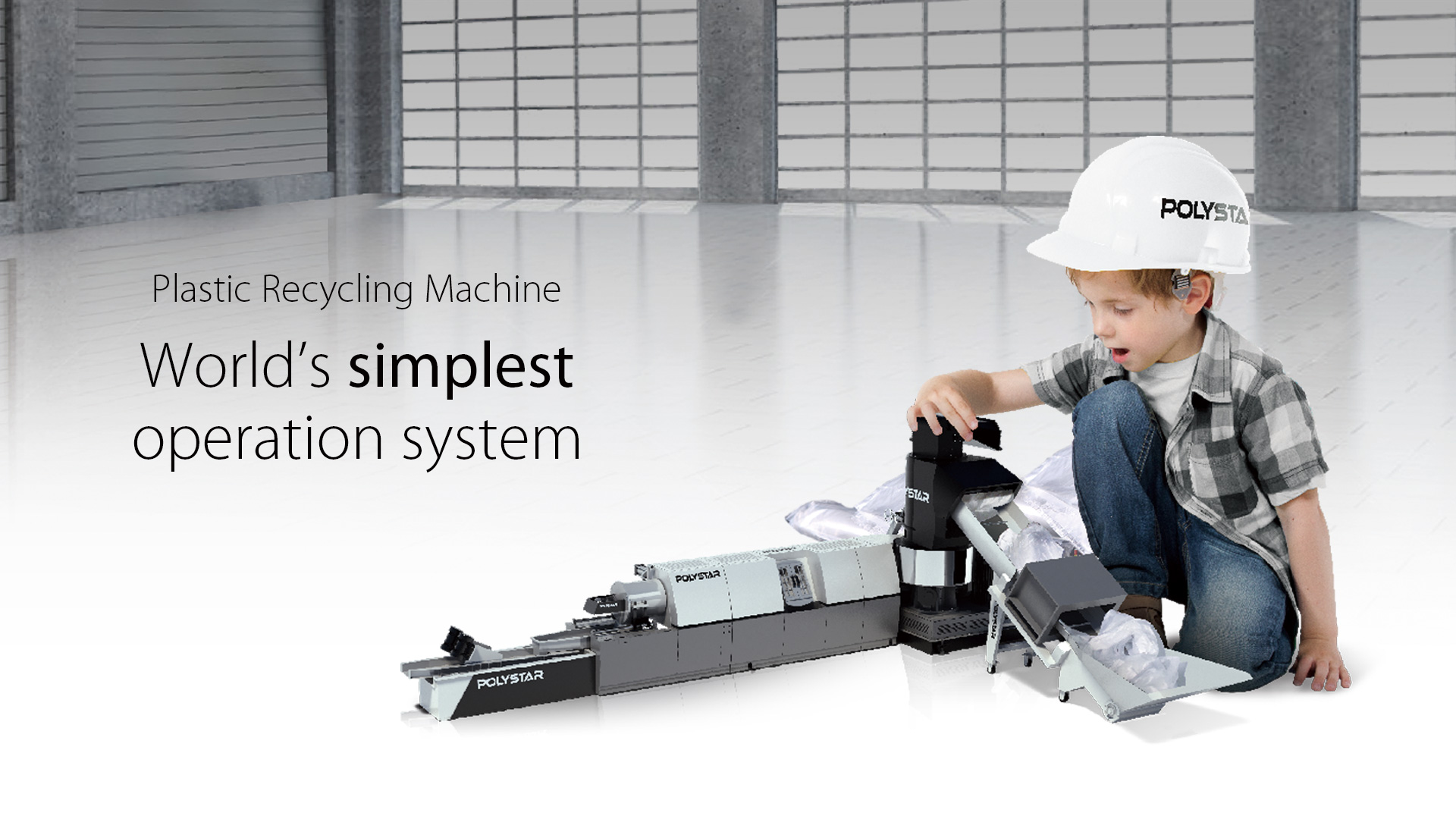 |
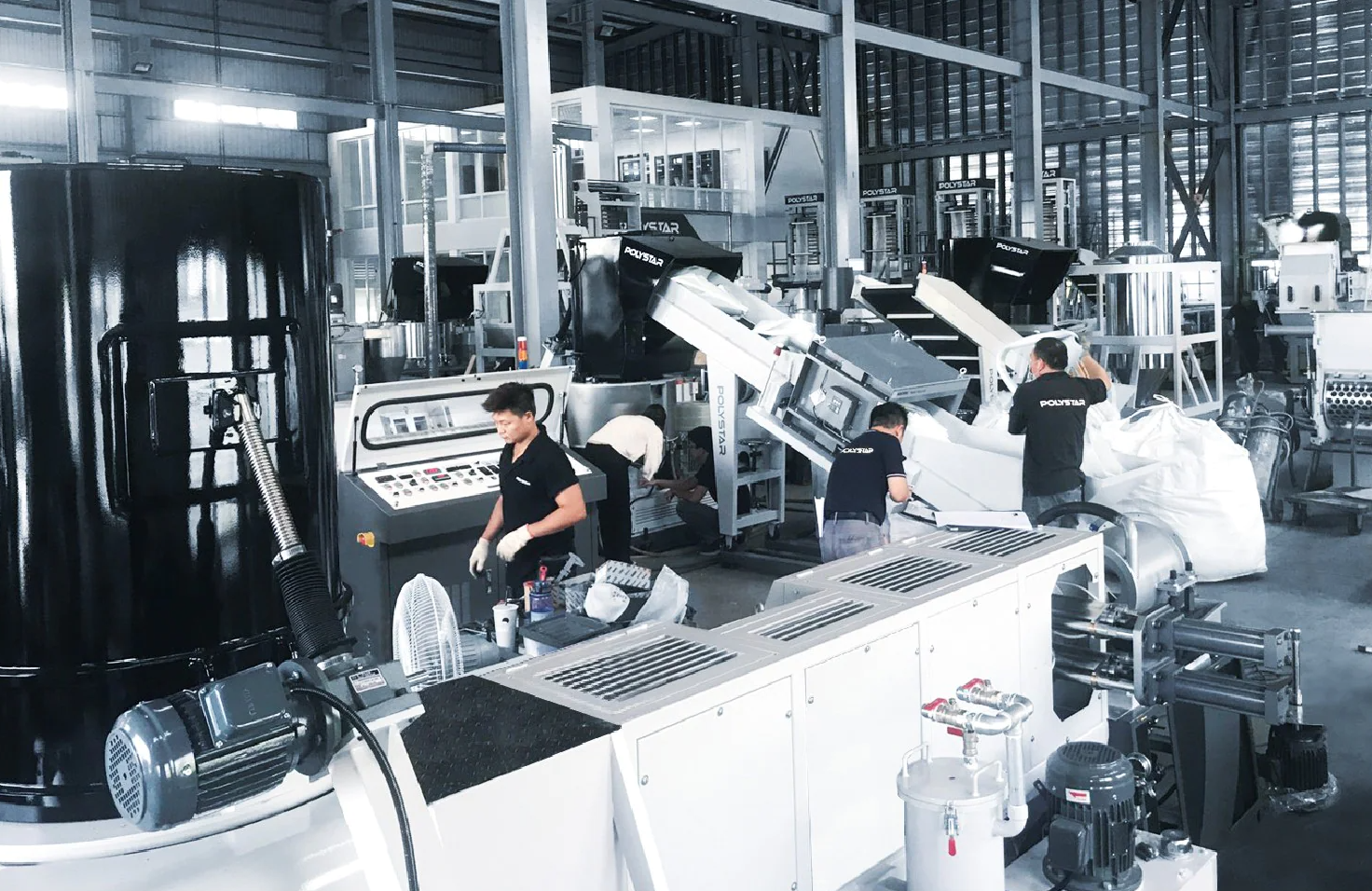 |
POLYSTAR advantage |
The design of the POLYSTAR pelletizing extruder is simple, and focused on the most important features for recyclers to have a stable operation in order to reduce down-time and lower production cost. Lower maintenance cost The cost of consumable parts is 2.5~3 times lower comparing to European machine suppliers of similar built quality.
Easy operation
The emphasis on easy user-interface makes sure that the Initial training time and cost for (new) machine operators can be greatly reduced. The simplicity in design also makes it easy for the operators to perform maintenance on the machine.
Less waste generated – thanks to faster change between different types of materials. Professional recyclers often times have to change between different types of materials with different shapes and colors. POLYSTAR unique design has a much less change over time (up to 30~40%) during the “purging” process and therefore generate less production waste comparing to other recycling extruders. |